AIR-COOLED DIESEL ENGINE
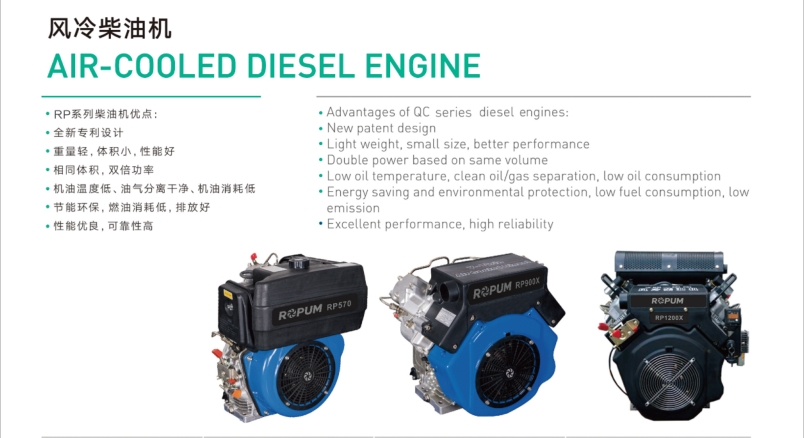
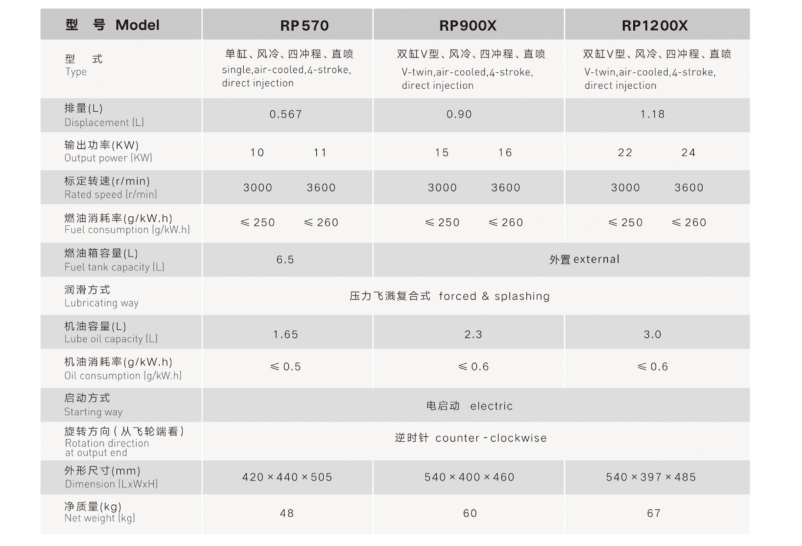
SAE Interface Abridged General View
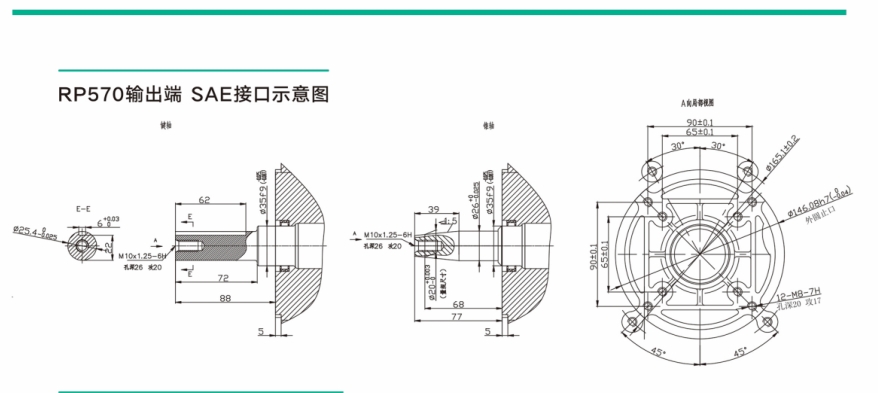
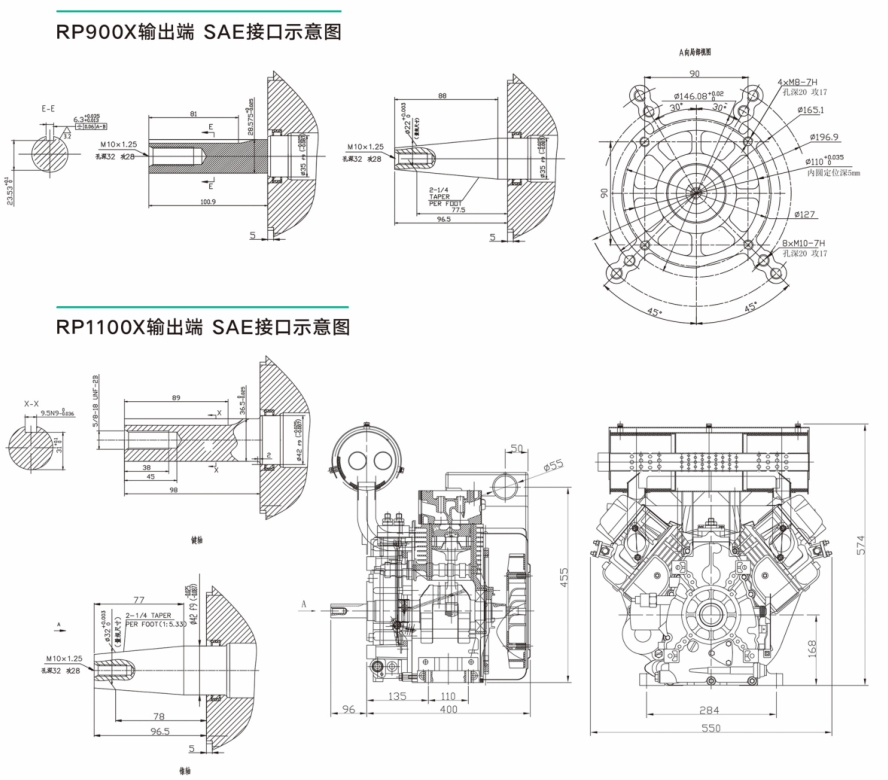
Maintenance key points of air-cooled diesel engine:
1. Clean the air cleaner
Air-cooled diesel engine depends on air cooling, and the cleaning of the air filter is crucial. Regularly clean or replace the air filter, because dust and other impurities if into the engine, will aggravate the parts wear. For example, after use in a dusty environment, the air filter is easy to block and should be cleaned in time. It is recommended to check every 50-100 hours.
2. Check the cooling fan and the guide hood
The cooling fan and air guide hood are key components of the air cooling system. To ensure that the fan blade is not damaged, deformed, and can rotate normally. The air shield shall be intact and tightly connected to ensure that the air can be effectively guided to the heating parts of the engine. If the fan is damaged, the cooling efficiency will decrease and the engine temperature is too high, the status of the fan and the guide hood should be checked once a month.
3. Oil inspection and replacement
Oil is the "blood" of the engine, and the oil level should be checked regularly. Too low oil level will affect the lubrication and heat dissipation effect. At the same time, the oil should be changed according to the prescribed cycle, because the oil will deteriorate after a period of use. In general, change the oil is operation every 100-150 hours or every 3-6 months (whichever comes first), and the oil level is checked before each use.
4. Fuel oil system maintenance
Clean the fuel filter regularly to prevent impurities from blocking the injection nozzle. In addition, the fuel tank should be kept clean to avoid the entry of moisture and impurities. After use in a humid environment, more attention should be paid to check whether the fuel system is flooded. It is recommended to clean the fuel filter every 200-300 hours and check the fuel quality each time the fuel is added.
5. Inspection and adjustment of valve clearance
The o-valve clearance varies with the use of the engine. If the valve clearance is not appropriate, it will affect the intake and exhaust of the engine, resulting in a decrease in power and increased fuel consumption. Generally, check and adjust the valve clearance every 300-500 hours to ensure the normal opening and closing time and lift of the valve.
6. Spark plug or injection nozzle check (for different types of engines)
For the gasoline air-cooled diesel engine, check the spark plug regularly. Spark plug electrode wear and carbon deposition will affect the ignition effect. For diesel air-cooled engines, check the fuel injection quality and atomization of the fuel injection nozzle. For example, the blockage of the fuel injection nozzle can cause uneven fuel injection and unstable engine operation. Spark plugs are recommended to be checked every 100-150 hours and the injection nozzle every 200-300 hours.


